Вал дымососа ТЭЦ НТМК (ОАО "Уралэнергоремонт").
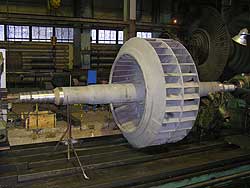 Рис.1. Вал дымососа после предварительной проточки |
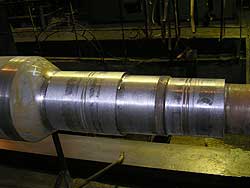 Рис.2. Вал дымососа после предварительной проточки (вид со стороны привода) |
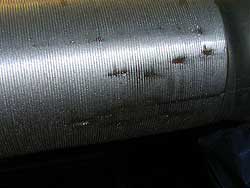 Рис.3. Часть поверхности после проточки на сторону до 1,5 мм (видны дефекты) |
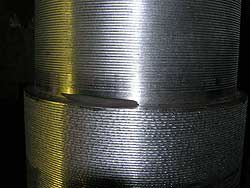 Рис.4. Выборка усталостной трещины шлифовкой |
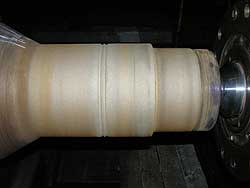 Рис.5. Вал после напыления перед проточкой "в размер" (Вид с опорной стороны ) |
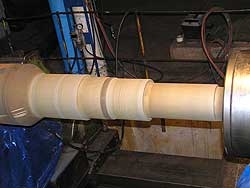 Рис.6. Вал со стороны привода перед окончательной проточкой |
Проблема
В процессе эксплуатации произошел износ опорных подшипников и вследствие этого произошел износ посадочных поверхностей на валах в местах посадки внутренних обойм подшипников.
На станции было принято неправильное технологическое решение — валы в местах износа были наплавлены дуговой наплавкой. Возможно, вследствие деформации или одновременно с этими шейками пришлось наплавлять примыкающие к ним поверхности под сальниками, а также хвостовик в месте установки полумуфты. На Рис.2 отчетливо видно что поверхность при точении обрабатывается неоднородно, что неопровержимо свидетельствует о присутствии закалочных структур, как в поверхностном слое, так и в местах изменения сечения вала. Вероятнее всего вал не подогревали до необходимой температуры (необходим подогрев до 200°С минимум), после наплавки отпуска не производилось.
После проточки и сборки, изделия некоторое время поработали, затем вследствие релаксации неснятых сварочных напряжений произошла деформация валов в процессе работы, что привело к вибрациям валов. По нормативам допускается биение в значимых сечениях не свыше 0,03 мм (на новых валах). При дефектации этих валов были установлены биения свыше 1,5 мм на сторону. Кроме того, из-за появления закалочных структур в местах упора внутренних обойм подшипников образовались усталостные трещины такой величины, что один из валов сразу же был списан в металлолом. На втором валу (см. Рис.4) трещина составляла по длине около 35 мм и глубиной до 5 мм.
Условия работы
Основной материал — углеродистая сталь 35, вал нормализован. Рабочее колесо из соображений сокращения сроков ремонта и снижения затрат не снималось (см.Рис.1). Требуется восстановление :
- со стороны привода:
- диаметр Ф180 — опорный подшипник,
- диаметры Ф200 и Ф170 — сальниковые уплотнения,
- диаметр Ф140 — устранение прогиба хвостовика полумуфты;
- со стороны рабочего колеса:
- диаметр Ф180 (опорный подшипник),
- диаметр Ф200 — сальниковое уплотнение.
Решение
Восстановление выборки усталостной трещины наплавкой по специальной технологии.
Восстановление выборки усталостной трещины производилось по специальной технологии в токарном станке c применением мобильного сварочного оборудования фирмы Kemppi. При этом температура предварительного подогрева составляла 100..120°С. При наплавке температура поверхности вала на расстоянии 30 мм от шва не превышала 70°С).
Газопламенное порошковое напыление всех дефектных поверхностей (шесть поверхностей) с последующей механической обработкой "в размер".
Все изношенные поверхности восстанавливались газопламенным порошковым напылением с применением мобильного оборудования для газопламенного напыления Сastodin 2000 фирмы Castolin-Eutectik. Абразивно-струйная обработка производилась с применением мобильного оборудования.
Напыление производилось композиционным материалом на основе механической смеси нескольких порошкообразных материалов, обеспечивающих наиболее оптимальное приближение по теплофизическим и металло-химическим свойствам к основному материалу и приемлемую обрабатываемость — включает хром, алюминий, никель, железо, медь, марганец.
Технико-экономический эффект
Восстановление дорогостоящего изделия из безнадежного состояния в течении 2 дней (исключая операции проточки). Сокращение потерь мощности блока (на 20%) из-за неработающего дымососа.
|